The mining industry is a cornerstone of the global economy, providing essential materials for countless industries. Within this vast sector, locomotives play a critical role, from hauling ore and transporting personnel to moving equipment within vast mining complexes. In this article we explore locomotive uses in the mining industry, challenges faced by diesel locomotives, and dive into how Automatic Engine Stop-Start (AESS) systems can mitigate these challenges and enhance the efficiency and sustainability of locomotive operations.
Uses of locomotives in the mining industry
Mining operations rely heavily on locomotives to ensure efficient and safe transportation of minerals, materials, and personnel within the underground environment. These powerful vehicles serve various purposes, each contributing to the smooth functioning of the mining industry. Their uses include, but are not limited to:
- Hauling Ore: Locomotives transport extracted ore from the mining site to processing plants, handling materials like coal, iron ore, copper, gold and more.
- Transporting Personnel: Locomotives shuttle miners and personnel within the mine, ensuring safe movement to work sites and emergency evacuation if needed.
- Moving Equipment and Supplies: Locomotives convey heavy machinery, equipment, and supplies within the mine, including drills, excavators, explosives, and construction materials.
- Ventilation and Maintenance: Equipped for ventilation, locomotives help circulate air in tunnels and transport maintenance crews and equipment for upkeep of infrastructure.
- Waste Removal: Locomotives haul waste materials, tailings, and overburden away from mining sites to designated disposal areas.
- Emergency Response: In emergencies, locomotives play a crucial role in evacuating miners swiftly and safely from hazardous conditions underground.
Efficiency and Sustainability in the Mining Industry
The mining sector's environmental footprint has come under intense scrutiny, and rightly so. The quest for efficiency and sustainability is not merely a trend but a necessity. In mining industry, efficiency is synonymous with cost-effectiveness, ensuring that resources are utilized to their utmost potential, minimizing waste, and reducing operational costs.
Sustainability, on the other hand, is our commitment to future generations. It involves adopting practices that ensure the long-term viability of natural resources and ecosystems. In mining, this means implementing technologies and processes that reduce emissions, conserve energy, and mitigate environmental impact.
There are a number of ways that mining companies can improve efficiency and sustainability. One way is to use more efficient mining equipment, such as locomotives equipped with Automatic Engine Stop-Start (AESS) systems. Another way is to improve mining practices, such as by optimizing haul routes and reducing idling time. Further down we explore the challenges faced by diesel locomotives used in mining industry and how AESS systems can help in overcoming them.
Challenges Faced by Diesel Locomotives in Mining
Diesel locomotives remain indispensable in mining operations due to their robustness, versatility, and reliability. In the rugged and often remote terrain of mining sites, diesel locomotives offer unmatched mobility, enabling the efficient transportation of heavy loads across varying landscapes. Their ability to operate independently of fixed electrical infrastructure makes them particularly suited for navigating challenging environments where power supply may be limited or non-existent.
Despite their indispensability, diesel locomotives are not without their challenges, particularly in mining operations. Some of the key challenges include:
- Maintenance and Reliability: Mining environments are rugged and can subject locomotives to extreme temperatures, dust, moisture, and vibrations. These conditions can lead to accelerated wear and tear on locomotive components, requiring frequent maintenance and repairs to ensure optimal performance and reliability.
- Fuel Efficiency: Diesel locomotives consume significant amounts of fuel, which can be a substantial operational cost for mining companies, especially in remote locations where fuel transportation may be challenging and expensive.
- Emissions and Environmental Impact: Diesel locomotives emit pollutants such as nitrogen oxides (NOx), particulate matter (PM), and carbon dioxide (CO2), contributing to air pollution and greenhouse gas emissions. Addressing these emissions is a growing concern for mining companies due to regulatory requirements and a focus on sustainability and environmental stewardship.
- Safety Concerns: The operation of diesel locomotives in confined underground spaces presents safety risks, including the potential for accidents, collisions, and exposure to harmful exhaust fumes. Ensuring the safety of miners and personnel working in proximity to locomotives is paramount and requires robust training, protocols, and safety measures.
- Operational Efficiency: Mining operations require efficient transportation of materials, personnel, and equipment within the mine site. Diesel locomotives must be capable of delivering the required hauling capacity and operating efficiently to meet production targets while minimizing downtime and delays.
- Regulatory Compliance: Mining companies must adhere to various regulations and standards governing the use of diesel locomotives, including emissions limits, workplace safety requirements, and transportation regulations. Compliance with these regulations adds complexity and costs to mining operations.
- Transition to Alternative Technologies: There is a growing trend towards the adoption of alternative propulsion technologies, such as battery-electric and hydrogen fuel cell locomotives, driven by concerns over emissions, fuel costs, and sustainability. Transitioning away from diesel locomotives presents challenges related to infrastructure, technology integration, and upfront investment costs.
These challenges highlight the need for technological advancements that can address these issues without compromising the critical functions that these locomotives serve.
Introduction to Automatic Engine Stop-Start (AESS) Systems
Automatic Engine Stop-Start systems are an innovative leap forward in locomotive technology. At their core, these systems automatically shut down a locomotive’s engine when it is not needed, and effortlessly restart it when it's time to resume operation. This simple yet effective approach can substantially reduce idle times and, consequently, the environmental and economic costs associated with running diesel engines.
These sophisticated systems are designed to be highly responsive, ensuring that the shutdown and restart processes do not impede the locomotive's operational readiness. They are equipped with a variety of sensors that monitor conditions such as engine temperature, air pressure, and battery charge to determine the optimal moments for engine shutdown and restart.
For a quick introduction to AESS systems you can read our article here: Automatic Engine Stop-Start (AESS) for Locomotives – Introduction
Benefits ofAutomatic Engine Stop-Start (AESS) Benefits
The integration of Automatic Engine Stop-Start systems into mining locomotives directly addresses both efficiency and sustainability concerns. These systems address several challenges related to the operation of diesel locomotives and offer multiple benefits that can be categorized into:
- Fuel Consumption and Costs: AESS systems can help reduce fuel consumption and operating costs by automatically shutting down the locomotive's engine when it's not in use, such as during idling periods or when parked. This prevents unnecessary fuel consumption, especially in situations where locomotives may idle for extended periods without actively hauling loads.
- Emissions Reduction: By automatically stopping the engine when it's not needed, AESS systems can help reduce emissions of pollutants such as nitrogen oxides (NOx), particulate matter (PM), and carbon dioxide (CO2). This contributes to improved air quality and environmental sustainability, addressing regulatory requirements and community concerns about emissions from diesel locomotives.
- Noise Reduction: Diesel locomotive engines can generate significant noise, particularly during idling. AESS systems can help reduce noise pollution in and around mining sites by automatically shutting down the engine when it's not actively powering the locomotive, leading to quieter operating conditions for workers and nearby communities.
- Engine Wear and Maintenance Costs: Continuous idling can accelerate engine wear and increase maintenance requirements, leading to higher operating costs and downtime for maintenance activities. AESS systems help minimize engine idling, extending the lifespan of locomotive engines and reducing maintenance costs associated with wear and tear.
- Compliance with Regulations: Many jurisdictions have regulations and emissions standards governing the operation of diesel-powered equipment, including locomotives. AESS systems can assist mining companies in meeting these regulatory requirements by reducing engine idling and emissions, thereby ensuring compliance with environmental and workplace safety regulations.
- Energy Efficiency: AESS systems can contribute to overall energy efficiency by optimizing the use of fuel and reducing unnecessary engine idling. This not only helps reduce fuel consumption and emissions but also improves the overall efficiency of locomotive operations, supporting sustainable mining practices.
- Operator Comfort and Safety: AESS systems can enhance operator comfort and safety by reducing exposure to engine noise, exhaust fumes, and vibration during idling periods. This can contribute to a more comfortable and productive working environment for locomotive operators, ultimately improving job satisfaction and safety outcomes.
- Improved Corporate Image: A significant benefit is the positive corporate image that comes with the adoption of green technologies. Companies that take proactive steps towards sustainability are often viewed more favorably by stakeholders, including investors, customers, and the communities in which they operate. This can lead to enhanced brand loyalty, a stronger social license to operate, and potentially, access to favorable financing options geared towards sustainable projects.
SmartStart AESS for Mining
SmartStart by ZTR is one of the most trusted AESS systems in the world offering all the benefits listed above along with verifiable fuel savings and splendid return on investment. It has been in operations for more than 30 years and is deployed on more than 10,000 locomotives globally. A SmartStart AESS system can save more than 30,000 liters of fuel in a year and has a positive return on investment in under 2 years.
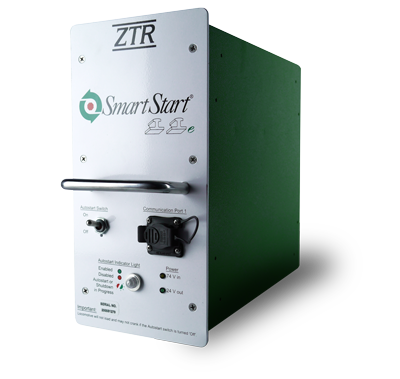
SmartStart is built on expandable technology to ensure that its benefits can evolve alongside changing industry demands. It comes with data connectivity feature SAVER that offers a comprehensive set of benefits for fleet management, fuel savings, and operational efficiency like GPS location, Geofencing, Fleet Reports and more.
Conclusion
In our pursuit of progress, the imperative for more efficient and sustainable mining practices becomes increasingly critical. Automatic Engine Stop-Start systems offer a powerful tool in this quest, providing a means to significantly reduce the environmental impact of diesel locomotives while enhancing operational efficiency.
Mining companies that embrace AESS technology stand to gain not only economic advantages but also enhanced environmental performance and community goodwill, positioning them for long-term success in the mining industry.